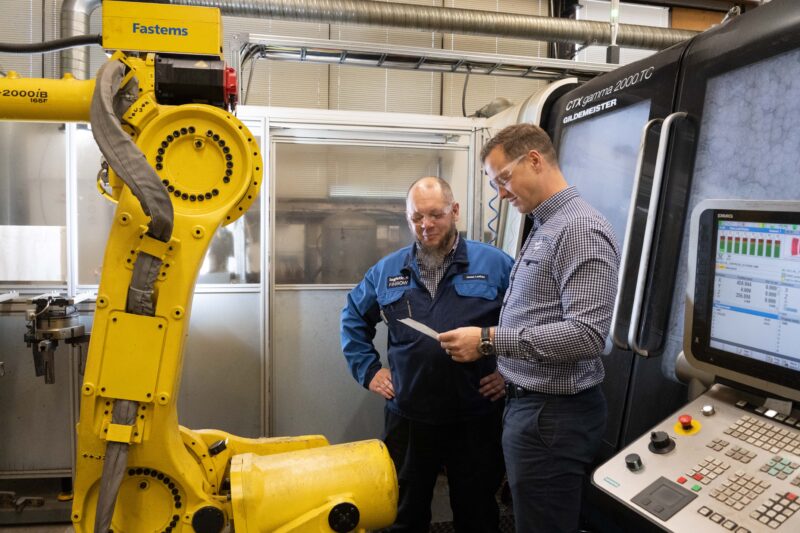
Modular thinking guides Finbow’s product development
Finbow is a global pioneer in spreader rolls and innovative solutions for the pulp and paper industry. Our products provide premium performance and durability, and as an assurance of Finbow quality, our rolls and service feature the best guarantees on the market.
The secret of our success is continuous product development that is firmly rooted in our varied experience of different operating environments. A part of our Finbow+ service model is performing detailed analysis on damaged rolls to learn how similar issues could be prevented in the future.
Here are some of the things we are currently working on to ensure that our rolls provide premium performance also in the future.
Bearings
Bearings are the most critical component in any spreader roll structure. Providing reliable performance requires a bearing design that meets the requirements of the roll’s operating environment.
“Having delivered over 3,000 spreader rolls worldwide over the years, Finbow has extensive experience in designing bearing solutions that stand the test of time and different conditions. We are still continuously improving our designs by analyzing 3D measuring data on bearing wear and finding new greasing solutions for different environments,” Finbow’s lead development engineer Jesse Laakso says.
Our innovative SmartBow is also being continuously developed. We are currently researching solutions that enable the SmartBow to be used in hot environments of up to 140° Celsius, new sensors for real-time analysis of the bow’s curvature, and solutions for remote reading and interference protection.
Couplings & Roll Ends
Moisture control is key in ensuring long service life for spreader rolls. Finbow rolls feature patented sealed couplings that are completely dirt and moisture proof and enable the roll to be used in damp positions. Our moisture control system eliminates the moisture inside the roll, which increases the lifecycle of the roll and ensures reliability.
We are also developing new sealing options and automatic greasing solutions to ensure that moisture cannot enter the roll from the ends of the shell.
Modular Design
Our latest spreader roll innovation is a new modular base design that makes customizing each spreader roll more straightforward. A multi-use basic roll design can be easily altered according to customer specifications with different threading/drive pulleys and mounting solutions.
“Modular design thinking enables mass tailoring, generates cost savings, and speeds” up delivery times. A uniform design also makes spare part deliveries considerably faster,” Jesse Laakso illustrates.
Coatings
Conventional spreader roll designs with plain chromium and rubber coatings attract stickies and grime. When longer running life, easy cleaning and increased drive times are required, we recommend our durable non-stick coating that guarantees maximum performance, premium rust resistance and easy cleaning. The NonStick T coating is recommended especially for spreader rolls in sizers and coaters.
A combination of Wolfram carbide and Teflon, the Finbow NonStick T coating is specially designed for spreader rolls in abrasive conditions. The double-layer coating provides excellent wear resistance and premium non-stick properties. We are also currently looking into options for replacing hexavalent chromium in our coating solutions in order to comply with future regulations and standards regarding its use.
Vibration control
Vibration control is essential in all rolls, but its importance is especially highlighted in rolls with high operating speeds. We are currently developing new tools for measuring and specifying vibrations already in the design phase. This way we can predict how the roll will behave in production and prevent possible malfunctions and unnecessary shutdowns even better.
What kind of new features would you like to see in our spreader roll solutions? Do not hesitate to contact us with any ideas or questions!